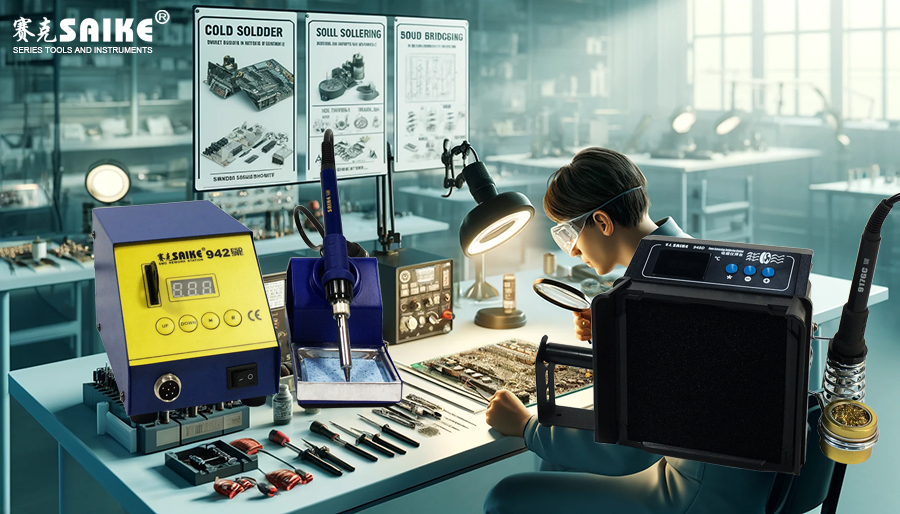
SK-YJ000HT-KP 100027
Soldering is a crucial process in electronic manufacturing, and the soldering quality directly affects the performance and reliability of the entire product. Soldering defects can not only degrade product performance but also pose safety risks. Therefore, identifying and preventing soldering defects on soldering stations is key to improving product quality, reducing costs, and enhancing customer satisfaction. This article will introduce the identification and prevention methods of soldering defects on soldering stations.
I. Types of Soldering Defects and Their Identification Methods
1.Cold Soldering
– Identification: Cold solder joints usually appear rough and dull, possibly presenting as globular shapes rather than typical peak or pad shapes. They may feel loose to the touch and can sometimes be easily removed by hand.
– Cause: Cold soldering is often caused by low soldering temperatures, excessive soldering speed, or inadequate cleaning of the workpiece before soldering.
2.Overheating
– Identification: The solder pads around overheated solder joints may turn yellow or discolor, and the soldering points may spread too widely, even damaging adjacent circuit board materials.
– Cause: The soldering temperature is set too high or the soldering iron stays too long on one solder joint.
3.Bridging
– Identification: Unnecessary solder connections are formed between two or more pins or solder pads, creating a bridge.
– Cause: Usually due to the use of too much solder or improper soldering techniques.
4.Weak Soldering
– Identification: The solder joint may appear normal, but the mechanical connection is weak, and the solder joint is easily broken under mechanical or thermal stress.
– Cause: The solder fails to properly wet the solder pad, possibly due to oxidation or contamination of the solder pad or component pin surface.
II. Prevention Methods for Soldering Defects
1.Correct Soldering Temperature Settings
– Ensure that the soldering station temperature is sufficient to fully melt the solder without overheating the components or excessively spreading the solder. Use a soldering iron thermometer to regularly check and calibrate the soldering station temperature.
2.Appropriate Soldering Speed
– The soldering speed should allow sufficient time for the solder to melt and flow correctly, rather than just touching the surface and quickly moving away. Practicing and mastering a stable and uniform technique is key.
3.Using Suitable Solder and Flux
– Choose solder and flux that are suitable for the job, ensuring that the flux can effectively remove the oxide layer, and the solder has an appropriate melting point and composition.
4.Clean Workpieces
– Clean all soldering surfaces, including solder pads and pins, before soldering. You can use a non-residual cleaner or alcohol to wipe them.
5.Training and Education
– Provide appropriate training to operators working on soldering stations to ensure they understand soldering techniques, the impact of soldering defects, and how to avoid common soldering problems.
6.Regular Maintenance of Soldering Station Equipment
– Ensure that the soldering station and its accessories (such as soldering iron tips) are regularly maintained and replaced to prevent soldering problems caused by equipment aging or damage.
III. Conclusion
Effective soldering defect prevention strategies require comprehensive consideration of equipment, materials, technology, and personnel training. By implementing the above measures, the occurrence of soldering defects can be significantly reduced, improving product reliability and production efficiency. Continuous monitoring and improvement of the soldering process will help maintain high-standard soldering quality and meet strict product requirements.