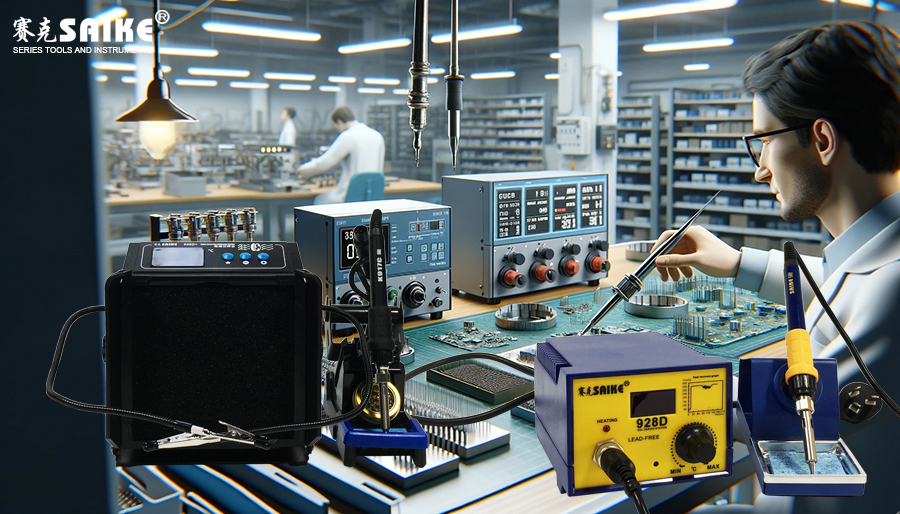
SK-YJ000HT-KP 100016
In the field of electronic soldering, soldering stations are often used alongside solder bars or solder wires to ensure optimal mechanical and electrical performance at the joints. Solder bars and wires play a crucial role in the soldering process, and their types and characteristics directly affect the quality and efficiency of soldering. This article will detail the types and characteristics of solder bars and wires used in soldering stations, helping users select suitable materials for their specific applications.
I. Basic Concepts of Solder Bars and Solder Wires
In electronic manufacturing, solder bars and wires refer to the filler materials used for soft soldering and brazing. They are primarily melted by heating through soldering stations, forming stable and conductive joints.
II. Types of Solder Bars and Solder Wires
1.Solder Bars
Solder bars are mainly used in wave soldering and dipping processes, commonly seen in large-scale production lines. Solder bars are rarely used directly in electronic soldering but more often serve as supplementary materials in soldering pots or baths.
– Tin-lead solder bars: Traditional solder bars containing different proportions of tin and lead (e.g., Sn60Pb40, Sn63Pb37). They have a relatively low melting point, making soldering easier.
– Lead-free solder bars: To meet environmental requirements, lead-free solder bars (e.g., Sn96.5Ag3.0Cu0.5) are widely used. They have a slightly higher melting point and are environmentally friendly.
2.Solder Wires
Solder wires are the most commonly used filler materials in electronic soldering, melted by heating the soldering iron tip of the soldering station to complete the soldering work.
– Tin-lead solder wires: Contain different proportions of tin and lead, offering good wettability and a low melting point, suitable for general electronic soldering.
– Lead-free solder wires: Typically consist of alloys such as tin, silver, and copper, meeting environmental standards. Despite their higher melting point, they provide higher mechanical strength and heat resistance.
– Flux-cored solder wires: These wires contain flux inside, which can be automatically released during the soldering process. This helps remove oxide layers and improves solder joint quality.
III. Characteristics of Solder Bars and Solder Wires
Temperature Characteristics
– Melting point: The melting point of solder bars and wires is a crucial factor when selecting soldering materials, affecting the temperature settings during the soldering process.
– Fluidity: Highly fluid solder can more easily fill soldering gaps, resulting in smooth, pore-free solder joints.
Mechanical and Electrical Characteristics
– Tensile strength: The mechanical strength of soldered joints directly affects the durability of the product.
– Conductivity: High conductivity solder ensures that the performance of electronic products is not affected by solder joints.
Environmental Impact
– Environmental standards: With increasing environmental regulations, lead-free solders have gradually become the industry standard.
– Reliability: Lead-free solders typically offer higher heat resistance and aging resistance than traditional tin-lead solders.
IV. Conclusion
Choosing the right solder bar or wire is crucial for successful soldering work. Users need to select suitable soldering materials based on melting point, fluidity, environmental requirements, and the desired mechanical and electrical characteristics. By correctly selecting and using solder bars or wires, soldering quality can be significantly improved, extending the lifespan of electronic products and ensuring compliance with environmental standards. Understanding and applying appropriate soldering materials is a key step in ensuring product quality and reliability in the electronic manufacturing and repair industries.