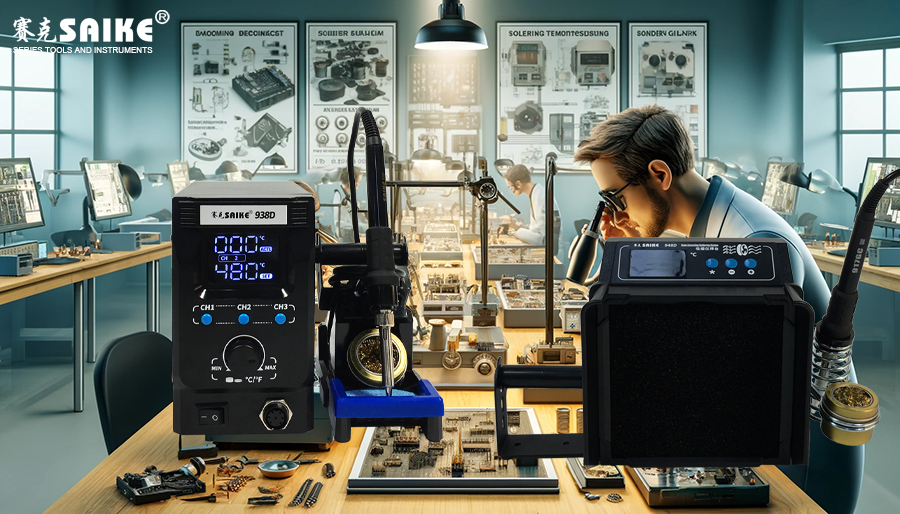
SK-YJ000HT-KP 100044
In the electronics manufacturing and repair industry, the quality of soldering on soldering stations directly affects the performance and reliability of products. However, various quality issues may arise during the soldering process, such as cold soldering, dry joints, excess solder, and solder joint fractures. Timely diagnosis and resolution of these issues are crucial to ensuring soldering quality. This article will introduce the diagnosis and treatment methods for soldering quality problems on soldering stations in detail.
I. Common Types and Diagnosis of Soldering Quality Issues
1.Cold Soldering
– Characteristics: Cold solder joints usually appear dull, rough, and lack luster, with weak soldering.
– Diagnosis: Check the appearance of the solder joints for smoothness and shininess; gently shake or pull the component to see if the connection is firm.
2.Dry Joints
– Characteristics: Dry joints may look normal, but the solder does not properly connect the component pins and pads.
– Diagnosis: Use a magnifying glass to observe whether there are cracks around the solder joints; gently pull or push the pins to check the stability of the connection.
3.Excess Solder
– Characteristics: Too much solder on the solder joints, which may cause short circuits or bridging between solder joints.
– Diagnosis: Check if the solder joints are abnormally protruding or if the solder connects adjacent pins.
4.Solder Joint Fractures
– Characteristics: The solder joints are completely or partially broken, often occurring in environments with high mechanical stress or frequent thermal cycling.
– Diagnosis: Perform visual inspections and micro-motion tests to confirm the integrity of the solder joints.
II. Treatment Methods for Soldering Quality Issues
1.Solving Cold Soldering and Dry Joints
– Adjust soldering temperature: Ensure that the temperature of the soldering station is appropriate. Typically, the temperature for soldering electronic components should be between 250°C and 350°C, with specific temperatures adjusted based on the type of solder used.
– Improve soldering technique: Use correct soldering techniques, such as heating the pads and pins first before introducing the solder. Ensure that the solder fully wets the soldering surface.
– Use suitable solder and flux: Choose high-quality solder and flux compatible with the component materials to ensure good solder flowability and wettability.
2.Handling Excess Solder
– Soldering technique adjustment: Control the amount of solder used to avoid excess. Use precise solder supply equipment such as solder paste or solder wire.
– Post-processing: If there is already too much solder on the solder joints, use a solder sucker or solder wick to remove the excess solder and then re-solder.
3.Preventing Solder Joint Fractures
– Mechanical reinforcement: Use additional mechanical fixation methods, such as glue or cable ties, at solder joints that may be subjected to mechanical stress.
– Avoiding thermal stress: Minimize the impact of thermal cycling during the design and soldering processes. Use temperature cycling tests to simulate and evaluate the performance of solder joints in actual use.
III. Conclusion
The quality assurance of soldering on soldering stations is achieved through careful operation, correct equipment settings, and continuous quality inspections. By diagnosing and addressing the aforementioned common soldering issues, the reliability and performance of products can be significantly improved. For soldering operators, continuous learning and improvement of soldering techniques are key to enhancing soldering quality. Additionally, adopting modern soldering equipment and materials is also an essential factor in ensuring soldering quality.