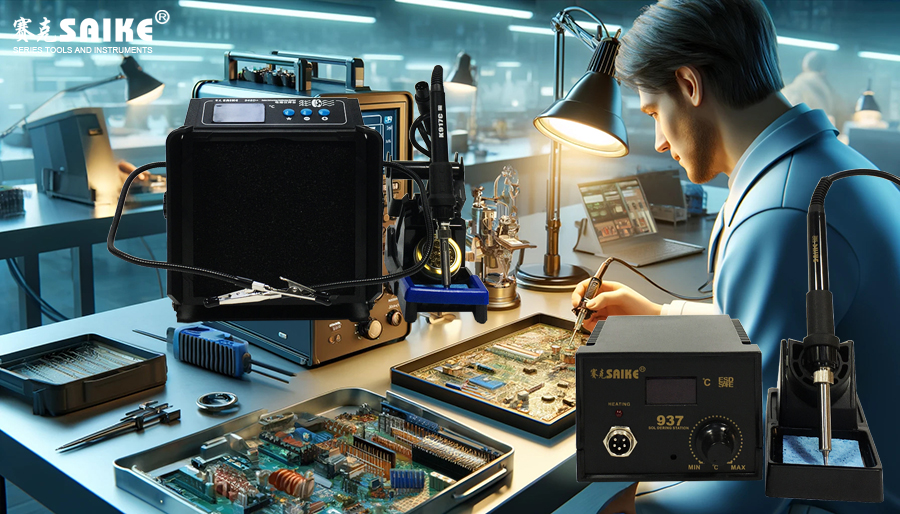
SK-YJ000HT-KP 100024
In welding operations, correctly grasping welding time and welding speed is one of the key factors to ensure the quality of solder joints. These two parameters directly affect welding efficiency, welding strength, and the reliability of the final product. This article will explore in detail how to effectively control welding time and welding speed when welding on a welding station to optimize the welding process.
I. The Importance of Welding Time
Welding time refers to the duration of contact between the soldering iron and the workpiece with solder. This time period is crucial for the melting, flow, and final solidification of the solder.
1.Excessive welding time: This can lead to overheating, affecting the performance of electronic components, especially temperature-sensitive ones. Excessive heating may also cause solder pad lifting or damage to the layers of the printed circuit board (PCB) around the solder joints.
2.Insufficient welding time: The solder may not fully melt or wet the welding area, potentially resulting in cold soldering or false soldering, leading to poor mechanical strength and easy breakage of the solder joints.
II. Controlling Welding Speed
Welding speed refers to the speed at which the operator moves the soldering iron. Appropriate welding speed ensures uniform solder distribution and forms a complete welded joint.
1.Excessive welding speed: This may result in the solder not fully filling all welding areas, leading to voids or weak connections in the solder joints.
2.Slow welding speed: This can cause local overheating, damaging the circuit board or causing excessive solder spread, affecting the appearance and function of the solder joints.
III. Techniques for Grasping Welding Time and Speed
1.Determining the appropriate welding time:
– Preheating: Before welding, preheat the welding station to the recommended welding temperature, usually higher than the melting point of the solder, to ensure rapid achievement of effective welding temperature.
– Practical experience: For typical solder joints, the recommended welding time is usually 1-3 seconds. The specific time is adjusted according to the type of solder, the size of the soldering iron tip, and the temperature setting.
2.Optimizing welding speed:
– Practice and observation: Feel the impact of different welding speeds on the quality of solder joints through practical operation. Observe the flow and filling of the solder to find the optimal movement speed.
– Technical guidance: Refer to the manufacturer’s technical documentation or seek advice from experienced welding technicians.
IV. Practical Application and Adjustment
1.Adaptability to different welding tasks:
– Small solder joints: More precise time control is required to avoid overheating damage.
– Large solder joints: A longer welding time may be required to ensure that the solder fully melts and evenly covers the joint.
2.Using timers and sensing technology:
– Timer: Some advanced welding stations are equipped with a timing function to help operators control welding time, especially suitable for repetitive operations on the production line.
– Temperature sensing technology: Some welding stations can automatically adjust the temperature through built-in sensors to adapt to changes in welding speed.
V. Conclusion
Correctly grasping the welding time and speed of the welding station is the key to achieving high-quality welding. Through careful practical adjustment and utilizing the functions provided by modern welding equipment, welding efficiency and product quality can be significantly improved. Continuous learning and practice, as well as continuous optimization of welding process parameterss, are the foundation for improving welding technology.