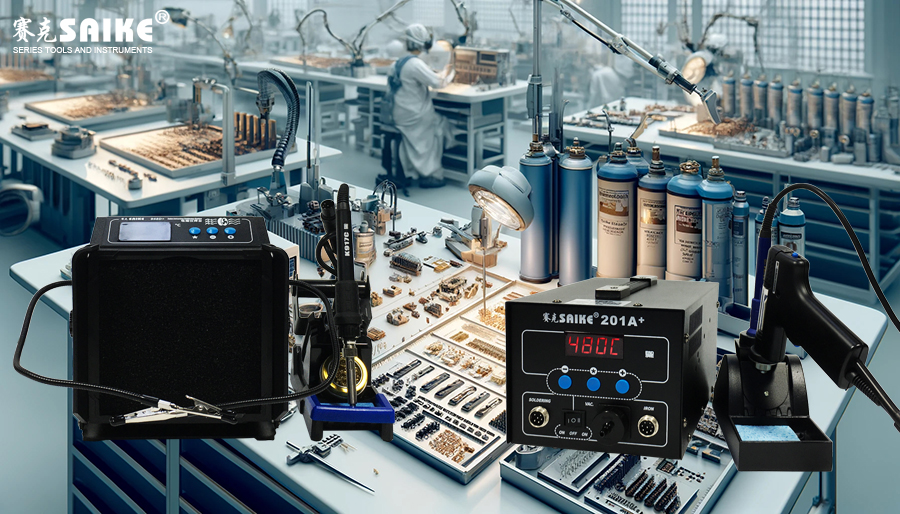
SK-YJ000HT-KP 100018
Flux and shielding gas play crucial roles in ensuring the quality of welded joints and preventing welding defects during the welding process. In the electronics industry, welding on welding stations often involves delicate welding operations. Using suitable flux and shielding gas can significantly improve welding efficiency, reduce defects, and extend product lifespan. This article will delve into the functions, selection criteria, and applications of flux and shielding gas in welding station welding.
I. The Role and Selection of Flux
1.Role:
The primary functions of flux are to aid in the flow and adhesion of solder through the following ways:
– Deoxidizing: Flux can remove oxides from metal surfaces and prevent the formation of new oxide layers.
– Improving wettability: By removing oxide layers, flux allows the solder to better wet the metal surface.
– Preventing re-oxidation: It provides protection during the welding process to avoid re-oxidation of the welded area.
– Providing thermal stability: It helps maintain the welded area within a suitable temperature range, avoiding overheating.
2.Selection:
Choosing suitable flux involves considering the following factors:
– Solder type: Different solders require matching flux types. For instance, lead-free solders often need more active fluxes.
– Application area: In electronic manufacturing, low-residue, low-corrosivity fluxes are essential to avoid damaging circuits.
– Cleaning needs: Select fluxes that require no cleaning or are easy to clean to reduce post-production workload and potential damage.
– Environmental and health considerations: Use fluxes that meet environmental standards and have minimal health impacts on operators.
II. The Role and Selection of Shielding Gas
1.Role:
During the welding process, shielding gas protects the welded area from harmful gases like oxygen and water vapor in the atmosphere. Its main functions include:
– Protection: It forms a gas barrier, preventing the welded area from contacting surrounding air and reducing oxidation and other chemical reactions.
– Stabilizing the arc: In arc welding, shielding gas can help stabilize the arc, improving welding quality.
– Controlling heat affect: It affects the heat input and distribution during the welding process by regulating heat transfer in the welded area.
2.Selection:
Choosing a suitable shielding gas involves considering the following factors:
– Welding material: Different base materials may require different shielding gases. For example, steel often uses a mixture of carbon dioxide or argon.
– Welding process: TIG welding commonly uses pure argon, while MIG welding may use a mixture of argon and carbon dioxide.
– Cost-effectiveness: The cost of the gas is also a consideration, and a balance needs to be found between cost and effectiveness.
III. Conclusion
Choosing and using the right flux and shielding gas in welding stations is crucial to ensuring welding quality and efficiency. Operators should carefully select flux and shielding gas based on specific welding materials, methods, and environmental requirements to optimize the welding process and ensure the quality and reliability of welded joints. With reasonable choices, not only can product performance be improved, but the environmental friendliness of the production process and the health and safety of operators can also be ensured.