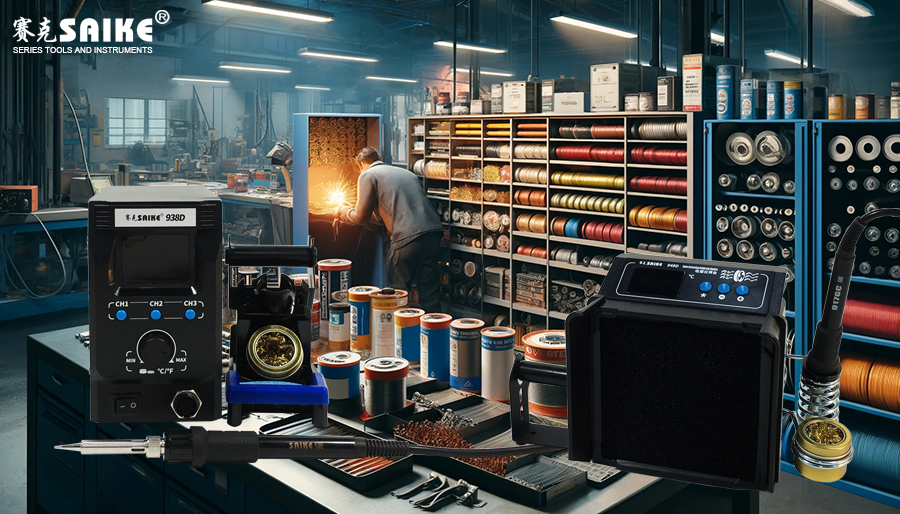
SK-YJ000HT-KP 100017
In the welding process, welding rods and wires are crucial materials. They not only affect the quality of the weld but also directly relate to welding efficiency and cost. Therefore, it is essential for welders to understand the different types of welding rods and wires and their characteristics.
I. Types and Characteristics of Welding Rods
1.Sodium Hydride Welding Rods:
– Characteristics: Suitable for welding stainless steel, magnesium alloys, and other materials. The weld seam has good surface finish, strong corrosion resistance, and air tightness.
– Precautions: Need to ensure storage in a dry environment to avoid moisture absorption.
2.Alkaline Welding Rods:
– Characteristics: Suitable for welding carbon steel, low-alloy steel, and other materials. It has a lasting potential effect, and the weld surface is smooth.
– Disadvantages: High residue and risk of corrosion.
3.Iron Oxidant Welding Rods:
– Characteristics: Suitable for welding iron, copper, copper alloys, and other materials. It has good wettability, and clear, distinct crystals can be observed on the weld surface.
– Precautions: Prone to slag formation in oxidizing environments.
II. Types and Characteristics of Welding Wires
1.Solid Welding Wires:
– Classification: Includes welding wires used for submerged arc welding, electroslag welding, CO2 gas shielded welding, argon arc welding, etc.
– Characteristics: Depending on the welding method and the welded material, the composition and properties of solid welding wires vary, but they usually have good conductivity and welding performance.
2.Flux-Cored Welding Wires:
– Characteristics: Can be used for welding carbon steel, low-alloy high-tensile steel, high-strength quenched and tempered steel, stainless steel, and hard-wearing steel materials. Due to the flux powder inside, flux-cored welding wires can form more beautiful and stronger welds during the welding process.
– Advantages: High welding efficiency, good weld quality, suitable for automated and semi-automated welding.
3.Active Welding Wires:
– Characteristics: In certain specific welding methods, such as TIG welding, active welding wires can improve the performance of welded joints by adding active elements.
– Applications: Mainly used in situations where there are special requirements for welded joints.
In addition, most welding wires on the market are rolled welding wires, including non-ferrous metal welding wires, stainless steel welding wires, carbon steel welding wires, alloy structural steel welding wires, low-alloy structural steel welding wires, etc. These welding wires have good conductivity and welding performance and are widely used in various welding occasions.
III. Summary
Understanding different types of welding rods and wires and their characteristics is crucial for selecting suitable welding materials and ensuring welding quality. When choosing welding rods and wires, it is necessary to comprehensively consider factors such as material characteristics, welding requirements, working environment, and cost. Meanwhile, with the continuous development of welding technology, new types of welding rods and wires will continue to emerge. Welders need to continuously learn and update their knowledge to adapt to new welding needs and challenges.