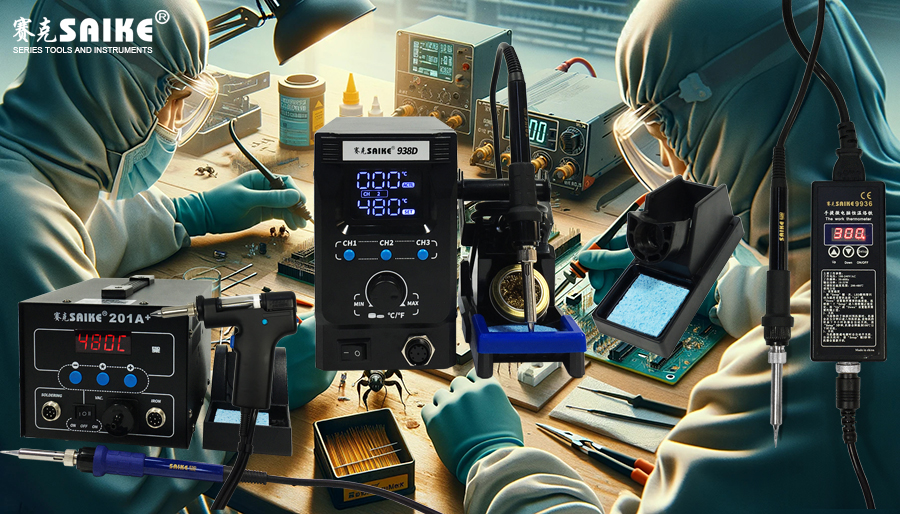
SK-YJ000DLT-KP 100021
In electronic production and maintenance, welding is an indispensable skill, and the handling of welding joints is an important part of the welding process. Proper handling of welding joints not only ensures the connectivity and stability of the circuit but also extends the service life of electronic equipment. The following will detail the handling skills and precautions of electric soldering iron welding joints.
I. Preparation of Welding Joints
1.Clean the joints:
– Before welding, make sure that the welding joints (including pads, pins, etc.) are clean.
– Use alcohol cotton or special cleaning agent to remove oil, oxides, or other contaminants on the joints.
2.Pin processing:
– For component pins, if there are signs of oxidation, use sandpaper or a specialized metal polishing cloth to gently remove the oxides.
– Ensure that the pins are straight, not bent or twisted, to facilitate accurate alignment and welding.
3.Pad processing:
– Check that the solder pads on the circuit board are intact and not damaged or contaminated.
– If there is residual solder or other substances on the solder pads, use a solder sucker or solder wire to clean them up.
II. Skills of Welding Joints
1.Preheating and positioning:
– Use an electric soldering iron to properly preheat the soldering points, which helps the solder flow and wet the joints better.
– Accurately align the component pins and solder pads to ensure good contact between them.
2.Feeding solder and heating:
– When the soldering iron tip reaches the appropriate temperature, contact the junction of the soldering iron tip and the soldering point with the soldering wire, allowing the solder to melt and flow into the joint.
– Keep the soldering iron tip in contact with the joint while continuing to heat until the solder completely melts and fully wets the soldering point.
3.Evacuation and cooling:
– Once the solder melts and wets the joint, quickly remove the soldering iron and soldering wire to avoid overheating and damaging the joint.
– Allow the soldering point to cool naturally. Do not touch the hot soldering point with your hands or tools to prevent deformation or stress.
III. Inspection and Repair of Welding Joints
1.Visual inspection:
– After welding is complete, first perform a visual inspection to ensure that the soldering points are smooth, full, and have no defects such as cold solder joints.
– Check for solder splashes or residues in undesirable places and clean them up in a timely manner.
2.Conductivity test:
– Use a multimeter or other testing tools to check the conductivity of the soldering points to ensure that the circuit is connected correctly.
3.Repairing poor welds:
– If poor welding is found, such as cold solder joints, the joint should be reheated, and appropriate solder should be added for repair.
– For shorts or bridges during the welding process, use a solder sucker or soldering wire to clean up excess solder in a timely manner.
IV. Precautions and Safety Protections
1.Safety protection:
– When welding, be sure to wear safety protective glasses to prevent splashes of solder or flux from injuring your eyes.
– If harmful gases are generated during the welding process, ensure good ventilation in the work area.
2.Use and maintenance of soldering iron:
– Regularly clean the residues on the soldering iron tip to maintain its good thermal conductivity.
– Use an appropriate soldering iron tip to avoid using too large or too small a soldering iron tip for welding.
3.Material selection:
– Choose high-quality soldering wire and flux to improve welding quality and reliability.
– Select the appropriate type of solder according to needs (such as leaded or lead-free).
V. Conclusion
By mastering the above-mentioned handling and skills of electric soldering iron welding joints, the welding quality and circuit stability can be effectively improved. Continuously sum up experience in practical operations and improve one’s welding skill level, which is crucial for electronic production and maintenance work.