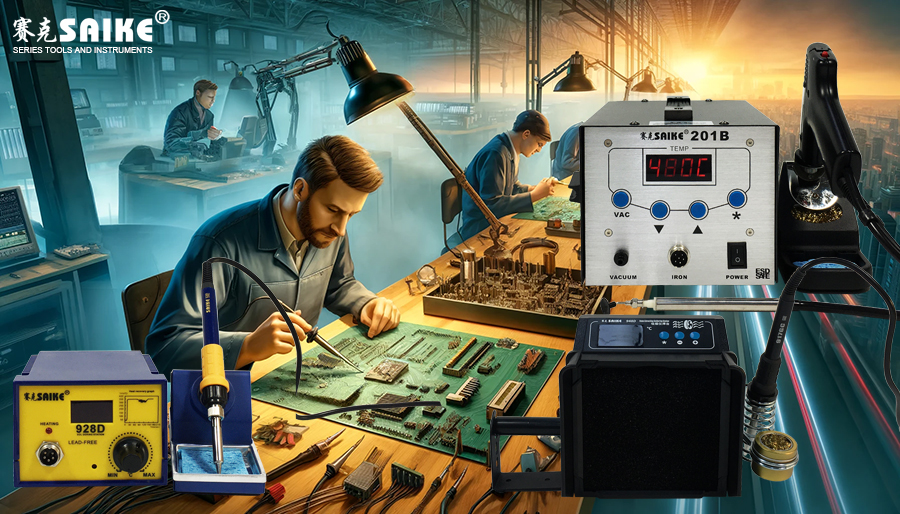
SK-YJ000DLT-KP 100005
The soldering iron is an indispensable tool in electronic production and electrical maintenance. It can effectively melt the solder and attach it to the soldering joint, thus completing the circuit connection or repair work. However, different application scenarios have different requirements for soldering irons. Therefore, correctly selecting a suitable soldering iron is crucial to ensure soldering quality and improve work efficiency.
Firstly, we need to consider the size and type of the soldering object. For delicate soldering work, such as soldering small components or integrated circuits, we need to choose a soldering iron with lower power and a thinner tip. This type of soldering iron can provide precise and concentrated heat, avoiding thermal damage to surrounding components. Conversely, for large soldering projects, such as soldering circuit boards or larger metal parts, we need to choose a soldering iron with higher power and a thicker tip to ensure that the soldering joints can melt quickly and uniformly.
Secondly, we also need to consider the type of soldering material. Different materials have different heat absorption and conduction capabilities, so it is necessary to select a suitable soldering iron based on the material characteristics. For example, when soldering metals with good thermal conductivity such as aluminum and copper, a soldering iron with higher power is required to provide sufficient heat to melt the solder. For thermally sensitive materials such as plastics and rubber, a soldering iron with moderate power and precise temperature control is needed to avoid material damage due to overheating.
In addition, the working environment is also a factor to consider when choosing a soldering iron. For example, when working in a damp or corrosive environment, we need to choose a soldering iron with waterproof and anticorrosion functions to ensure stable and reliable operation. At the same time, for scenarios that require long-term continuous work, we should also choose a soldering iron with a longer service life and better heat dissipation performance.
Apart from the above points, there are some other factors to consider. For example, whether a soldering iron with temperature adjustment is needed to adjust the temperature of the soldering iron tip according to the soldering requirements; whether a soldering iron with a solder suction function is needed to clean the excess solder on the soldering joints during the soldering process; and whether a soldering iron with anti-static function is required to avoid damage to electronic components caused by static electricity.
In summary, selecting a soldering iron requires comprehensive consideration based on different application scenarios. We need to choose a suitable soldering iron based on the size and type of the soldering object, the characteristics of the soldering material, the requirements of the working environment, and other specific needs. Only in this way can we ensure the smooth progress of soldering work and improve soldering quality and work efficiency.
Finally, it should be emphasized that regardless of which soldering iron we choose, we should follow the correct usage methods and safety operation procedures. When using the soldering iron, keep the soldering iron tip clean and intact to avoid oxidation or damage that affects the soldering quality; at the same time, pay attention to electrical safety to avoid accidents such as electric shock or fire. Only by correctly selecting and using the soldering iron can we better complete electronic production and electrical maintenance work.